先進粉末高溫合金製備工藝(yì)詳解_鎳基高溫合金粉
點擊量(liàng):2283 發布時間:2016-12-23 作者:快猫视频APP下载安装(上海)增材製造技術有限公司
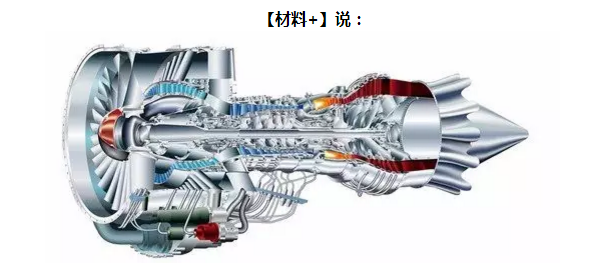
粉末高溫合金是製造(zào)高(gāo)性能航空(kōng)發動機渦(wō)輪盤等轉動部件的關鍵材料(liào)。針對國(guó)外粉末高溫(wēn)合金的研究曆史和現狀,結合粉末高溫合金的製備工藝流程,重點對比分析(xī)了國內外不(bú)同粉末製備工藝(yì)、粉末固結工(gōng)藝、盤件成形(xíng)工藝的特點。
由於高溫合金(jīn)具有合金化(huà)程度高的特點(diǎn),鑄錠偏析問題十分突出,熱加工性能差,采用傳統的鑄鍛工藝很(hěn)難成型。而粉末高溫合金(jīn)利用粉末冶金方(fāng)法製備高溫合金,具有成分均勻,無宏觀偏析,製(zhì)件性能穩定,熱加(jiā)工變形性能較好等優點。因此(cǐ),粉末高溫合(hé)金在各個領域(yù)都具有廣闊的發展前景[1]。
上世(shì)紀60年代初,隨著快速(sù)凝固氣霧(wù)化粉末(mò)製備技術的興(xìng)起,1965年發展了高純預合金粉末製備技術[2]。美國P&WA(Pratt&WhitneyAircraft)公司首(shǒu)先將Astroloy合金製成預合金粉末,成功地鍛(duàn)造出力學性能相當或略高於鑄鍛高(gāo)溫合金Waspaloy的盤件,開創(chuàng)了(le)粉末高溫合金盤件用於(yú)航空(kōng)發動機的先(xiān)河。P&WA公司於1972年將IN100粉末高溫合金製備的壓氣機盤和(hé)渦輪(lún)盤等11個部件用於F100發動機,裝配在F15和(hé)F16飛機上,從此粉(fěn)末高溫合金(jīn)進入了實際應用階段。
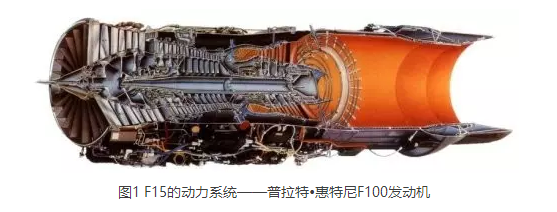
為滿足新一代航空發動機的需求,相繼出現了由美國國(guó)家航空航天局(NASA)、普惠、通用公司(sī)合作開發的Rene104高溫(wēn)合金、Honeywell公司開發出來(lái)的Alloy10高溫合金以及由NASA幵發的LSHR高溫合金等眾多具(jù)有優良綜合性能的粉末鎳基高溫合金。Rene104合金與(yǔ)美國其(qí)他粉末冶金高溫合金的製備工藝類似,釆用氬氣霧(wù)化工藝製備合金粉末,之後壓實成形(xíng),通過熱擠壓獲得完全再結(jié)晶組織的棒料,再(zài)通(tōng)過超塑性等溫鍛造工(gōng)藝獲得零部件毛坯,經過熱處理和機加工獲得最終的零部件。
美國鎳基粉末(mò)高溫合金生產工藝的特點主要(yào)在於其(qí)特殊的合金粉末製(zhì)備方法,即氬氣霧化法,以(yǐ)及隨後進行的“熱(rè)擠壓(yā)+等溫鍛造”工(gōng)藝成(chéng)型,該(gāi)工藝製備的(de)零部件組織均(jun1)勻,無宏觀偏析,熱加工性能好。
俄羅斯幾乎與美國在同一個時期開始該(gāi)合金的研製(zhì)工作,在(zài)這一領域進行了開拓性的研究工作,發展了具有自身特色的鎳(niè)基粉末高溫合金製備技術,並取得了(le)重要成果。
蘇聯的全俄輕合金研究院(yuàn)在20世(shì)紀80年代成立了粉末高溫合(hé)金研發實驗室,開始研製鎳基粉末(mò)高(gāo)溫合金。從此(cǐ),蘇聯(lián)在粉(fěn)末高溫合金領(lǐng)域占據了(le)一席之地。蘇聯製備粉末高溫合(hé)金的主要工藝與美國(guó)大不相同:高(gāo)溫合金電極棒的製備一等離子旋轉電極(jí)霧化製粉一粉末預處理(lǐ)一包套封焊及除氣一熱(rè)等靜壓(yā)成型一熱處理一機(jī)加工一(yī)成品。
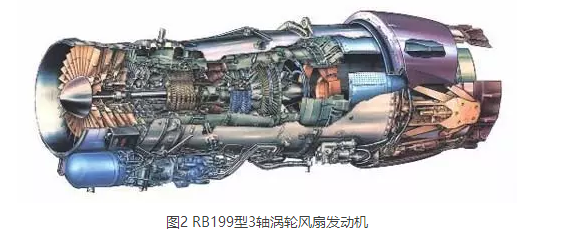
英、法等國在鎳基粉末高溫(wēn)合金研製領域也同樣展開了研究工作[3]。英國威合金公(gōng)司(WigginAlloys)在1975年裝備了一條年產1000t粉末高溫合金的生產線,同時配備了熱等靜壓機及等溫鍛造(zào)機。英國(guó)羅羅公司(Rolls-Royce)和威合金公司合(hé)作,成功研製出AP-1鎳(niè)基粉末高溫合金(jīn),並應用(yòng)在RB211發動機上,隨後(hòu)德國默透公司將該合金用(yòng)於RB199發動機(jī)上。法國通過調整Astroloy合金的成分,進(jìn)一步將低碳含量,研製出N18鎳基粉末高(gāo)溫合金,並用於M88發動機上。隨後,法國又陸續開(kāi)發了N19、NR3、NR6等粉末高溫合金。
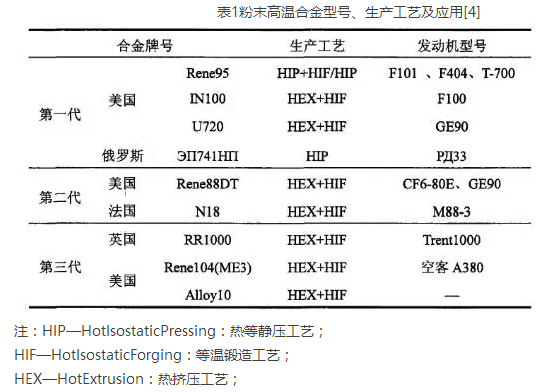
目前我國已經形成(chéng)了等離子旋轉電極(jí)霧化製粉+熱等靜壓成型+包套鍛(duàn)造+熱處理”的鎳基粉末高溫(wēn)合金製備工(gōng)藝路線。
美國粉末高溫合金組織均勻、性能穩定,其工(gōng)藝的主要特點是釆用氬氣霧化製粉+熱擠壓+等溫鍛造成型。而俄羅斯開創了粉末高溫合金製備工藝的又一領(lǐng)域,其粉末(mò)高溫合(hé)金的生產工藝是:合(hé)金熔煉及加工電極+等離子旋轉電(diàn)極製備合金粉末+粉末處理+包套製作及封焊(hàn)+熱等靜壓成型+熱處理(lǐ)+機加工(gōng)[4]。
我國粉末高溫合金的製備(bèi)工藝在借鑒俄羅斯的基礎上,進行了(le)適合我(wǒ)國國情的調整。生產粉末高溫(wēn)合金(jīn)的一般工藝流(liú)程(chéng)如下:
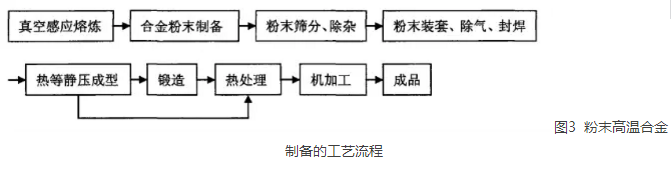
圖3 粉末高溫合金(jīn)製備的工藝(yì)流程
1、粉末製備工藝
目前為止,高溫(wēn)合金製粉方法中最重(chóng)要的就是霧化法。19世紀30年代(dài),霧化(huà)法被首次應(yīng)用在鐵粉製備領域。經過幾十年的發展,該方法仍(réng)然是製備合金粉末的重要方法(fǎ)。
目前在(zài)實(shí)際生產中主要(yào)采(cǎi)用氬氣霧化法(AA)和等離子旋轉電極霧化法(PREP),示意(yì)圖如圖4所示[6]。
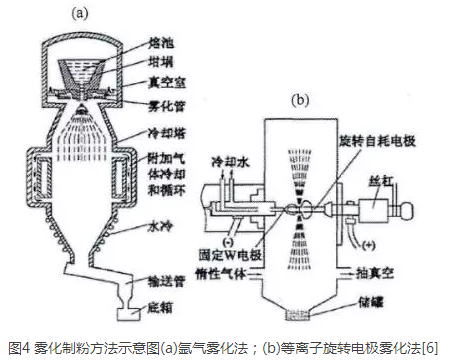
氬氣霧化法是用氬氣吹噴融化的高溫合金流,而製得合(hé)金粉末。如圖4(a)所示,氬氣霧化係統含有一套很長的(de)冷卻塔,冷卻塔的頂部安裝了噴嘴(zuǐ),可以噴(pēn)出高壓的氬氣,使熔化的金屬被迅速分散成液滴。霧化過程中氬氣的熱擴散可能會導致氣壓差,使噴嘴處氬(yà)氣(qì)停流(liú),為了(le)避免這種(zhǒng)情況出現,多餘的氬氣將(jiāng)在冷卻塔重(chóng)新冷卻、回(huí)流到熔化室。這使得將大體積鑄錠霧化成粉得以實現。在實際霧化(huà)過程中,熔化室和冷卻塔之間會保持約0.2atm的壓差。凝固的金屬(shǔ)顆粒在霧化(huà)係統底部的冷卻區域進一步被冷卻,並被輸送到一係列的手套箱中進行粒度篩分。
等離子(zǐ)旋轉電極霧化製粉法(fǎ)不僅可以霧化(huà)低熔點的金屬和合金,還可以製取難熔(róng)金(jīn)屬粉末。如圖4(b),將(jiāng)要霧化(huà)的金屬或合金製備成直徑50mm圓棒狀旋轉自耗電極,固定在送料器上,通過真空(kōng)泵(bèng)將粉末收集室先抽成真空,然後充入氬氣,使粉末收集室內保持氬氣微正壓,通過固定的(de)鎢電極產生電弧使金屬或合(hé)金熔化。當自耗電極(jí)快(kuài)速旋轉時(shí),離心力使熔化的金屬或合金(jīn)液滴飛出,熔滴(dī)在尚未碰到收集室器壁以(yǐ)前,就凝(níng)固於惰性氣體(tǐ)氣氛之中(zhōng)。旋轉(zhuǎn)電極轉速在10000-20000r/min之間,生產的粉末粒(lì)度較大。由(yóu)於等離子旋轉電極霧化法不受(shòu)熔化坩堝的汙染,生產的粉末十分(fèn)純淨(jìng),尤其適(shì)用於高溫合金的製備。
在高溫合金粉末工業(yè)生(shēng)產中,美國和(hé)西方國家主要使用AA法,俄羅斯使用(yòng)PREP法,我國使用PREP法和AA法。2種製粉方法特性比較[7]見表2。
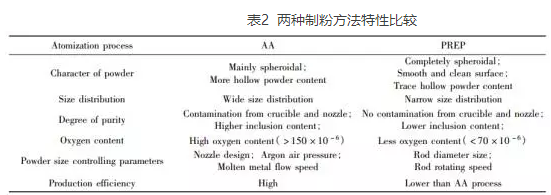
2、粉末固結(consolidation)工藝
由於高溫合金粉末往往含有(yǒu)Cr,Ti,Al等難燒結元素,同時這些元素在燒結溫度下容易氧化,這造成了高溫合金粉末(mò)不能(néng)采用通常的直接燒結工藝來成形。對於粉(fěn)末高溫合金來說,往往要求(qiú)在(zài)高溫高壓的(de)環境下成(chéng)形。目前常(cháng)用的有真空熱壓成形(VacuumHotPressing)、熱等靜(jìng)壓(yā)成形(HotIsostaticPressing)、電火花燒結(SparkSintering)、擠壓(Extrusion)、鍛造(Forging)等成(chéng)形(xíng)方法。在上述粉末固結工藝中,粉末渦輪盤用得最多的是熱等靜壓(yā)成形和熱擠壓。表3為高溫合金粉末(mò)不同固(gù)結工藝的特(tè)點對比[8]。
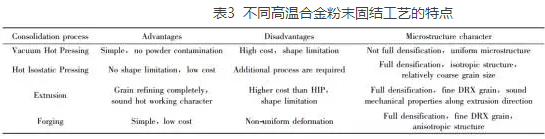
熱擠(jǐ)壓成形在歐美等國應用較多,由普惠公司首先使用,美國大部分鎳基粉末高溫合金(jīn)都采用該(gāi)方法成形。該方法是直(zhí)接將合(hé)金(jīn)粉末擠壓成坯體(tǐ),合金粉末在真空下裝入包套在擠壓過(guò)程中成型(xíng)。髙溫擠壓成型的過程中(zhōng),包套內的粉末顆粒變形量大、變形程度高,粉末顆粒承受剪切(qiē)力和熱壓(yā)力,使粉末(mò)中的枝晶破碎。由此方法得到的合金(jīn)晶粒細小,具有一定(dìng)的超塑性。將材料在細晶超塑性狀態下鍛造成型,再通過熱處理得到力學性能良好(hǎo)的(de)高(gāo)溫合金。
英美等發達國家也有采用熱等靜壓+等溫(wēn)鍛造的工藝使粉末高溫合金成型。該(gāi)方法由通用公司首先采用,等溫鍛造是鍛造的一種形式,將合金粉末在真空下裝入包套並熱等靜壓成型,隨後將成型之後的包套(tào)放在模具中,以較慢變形速率進行熱變形。其特點是晶粒(lì)細小,組織(zhī)均勻,精度高,節省材料,降低機加工成本。同時,等溫(wēn)鍛造也存在(zài)一(yī)些缺點,比如,模具(jù)材料及其加工成(chéng)本(běn)高,生(shēng)產效率較低(dī),鍛造條件要求(qiú)較高,引起高(gāo)成本等。
我國目(mù)前尚沒有大型(35000)立式擠壓機,不能采用熱擠壓+等溫鍛造的工(gōng)藝。北京航空材料研究院和北京鋼鐵研究總院等單位均(jun1)配備了(le)大型熱等靜壓機,但等溫鍛造設備及模具等關鍵問題(tí)尚不能完全解決。目前,我國在製備鎳(niè)基粉末高溫合金方麵多釆用直接熱等靜壓成型或熱等靜壓(yā)+包套鍛造工藝,同時也在(zài)發展等溫鍛造(zào)。
對於熱等(děng)靜壓工藝,一般工藝流程是將處理(lǐ)後的高溫合(hé)金粉末裝(zhuāng)入碳鋼或不鏽鋼(gāng)包套(tào)中(zhōng),並抽成真空,在常溫或一(yī)定溫度(dù)下使粉末繼續除氣,然(rán)後封焊。將封好的包套置入熱等靜(jìng)壓爐中(zhōng),升溫至一定溫度保溫,以一(yī)定的氬氣保持壓力(lì)。
從而使粉末達到致密的狀態,並具備所需要的力學性能。直接熱等靜壓成型的工藝取得成(chéng)功,降低成本(běn)左右。發動機上使用的零件,至今仍采用直接熱等靜(jìng)壓狀態的零件。
在上述粉末固結工藝中,熱等靜壓和熱擠壓是主要的密實(shí)工(gōng)藝。這兩種工藝都是在一定的溫度和壓力下的粉末熱塑性變形和再結晶過(guò)程,但是熱擠壓工藝的(de)粉末變形量和變形速率更大。
3、盤件成形工藝
盤件成形工藝[9]主(zhǔ)要有直接熱等靜壓成形和鍛造成形,對於直接熱等靜壓成形生產的粉末盤件,粉末固結和盤件成形是在同一HIP工序中完成的。俄羅斯粉末高溫合金的主導成形工藝是直接熱等(děng)靜壓(As-HIP)成形,在熱等靜壓過程中材料收縮(suō)和應力狀態的研究及包套的計算機模擬輔助設計等方(fāng)麵都居世界前列,經過(guò)四十餘年的發展,HIP成形工藝日趨完善。與俄羅斯相比,美國粉末盤件的成形工藝種類更為豐富,包括(kuò)As-HIP成形、熱模鍛、ITF(等溫鍛)等工藝。我國(guó)的粉末高溫合金盤件采用直接熱等靜壓成形和鍛造成形2種工藝製備[10]。FGH97粉末盤(pán)件的製備工藝流程與俄羅斯EP741NP合金完全相同,采(cǎi)用直接熱等靜壓工(gōng)藝成形。
上(shàng)一篇:工業3D打印“叫好不叫座”:便宜材料幹不(bú)了事(shì) 能幹事的又太貴